Identification of faults in rotating machines using high precision FBG vibration sensor: a case study on PM schemes
Indonesian Journal of Electrical Engineering and Computer Science
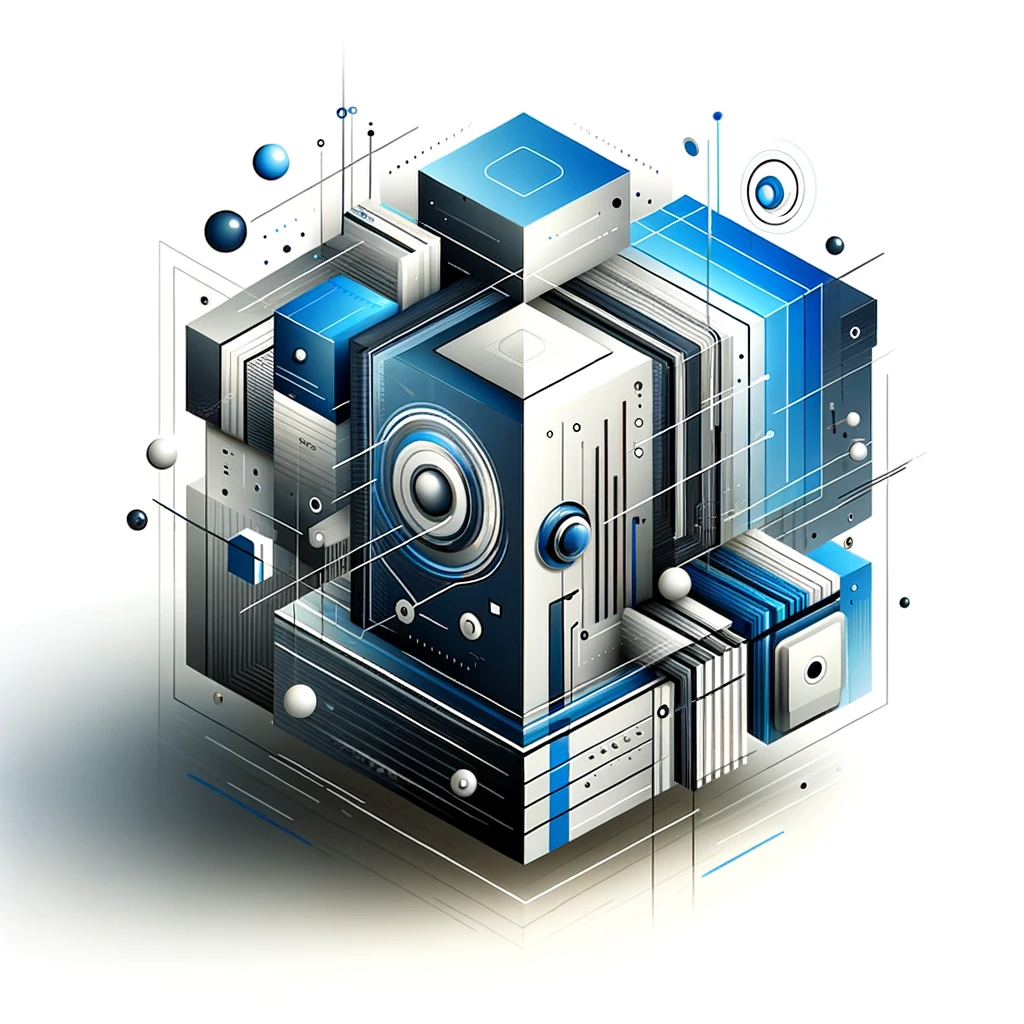
Abstract
Predictive maintenance (PM) is a data-driven approach to performing proactive maintenance by analyzing the condition of the equipment in any industrial setting. The high-precision sensors are widely adapted to meticulously analyze critical maintenance conditions using such a data-driven approach. In a similar context, a fiber brag grating (FBG) sensor is a passive and high-precision sensor that is widely used in industries where conventional sensors are not preferred. Broadly, this article presents four sub elements of the proposed integrated system such as the design of the sensor element, signal processing scheme (SPS), machine learning (ML) model for predicting anomalies, and decision support system (DSS) to suggest maintenance actions. Also, this article highlights an experimental case study on vibration monitoring and analysis of real-time signals for making proactive maintenance decisions. An FBG vibration sensor of center wavelength 1,550 nm is designed and utilized to acquire real-time vibration signatures of a rotating machine under test. A piezoelectric vibration sensor is used with the FBG sensor to compare the vibration response obtained during the test. Pre-processing of raw signals is performed using a moving average filter (MAV) followed by a low pass filter to nullify the effect of noise. To obtain proactive maintenance decisions, a DSS model is prepared by considering the processed vibration signatures. Various maintenance conditions are tested during the experimental analysis and detailed results analysis are presented.
Discover Our Library
Embark on a journey through our expansive collection of articles and let curiosity lead your path to innovation.
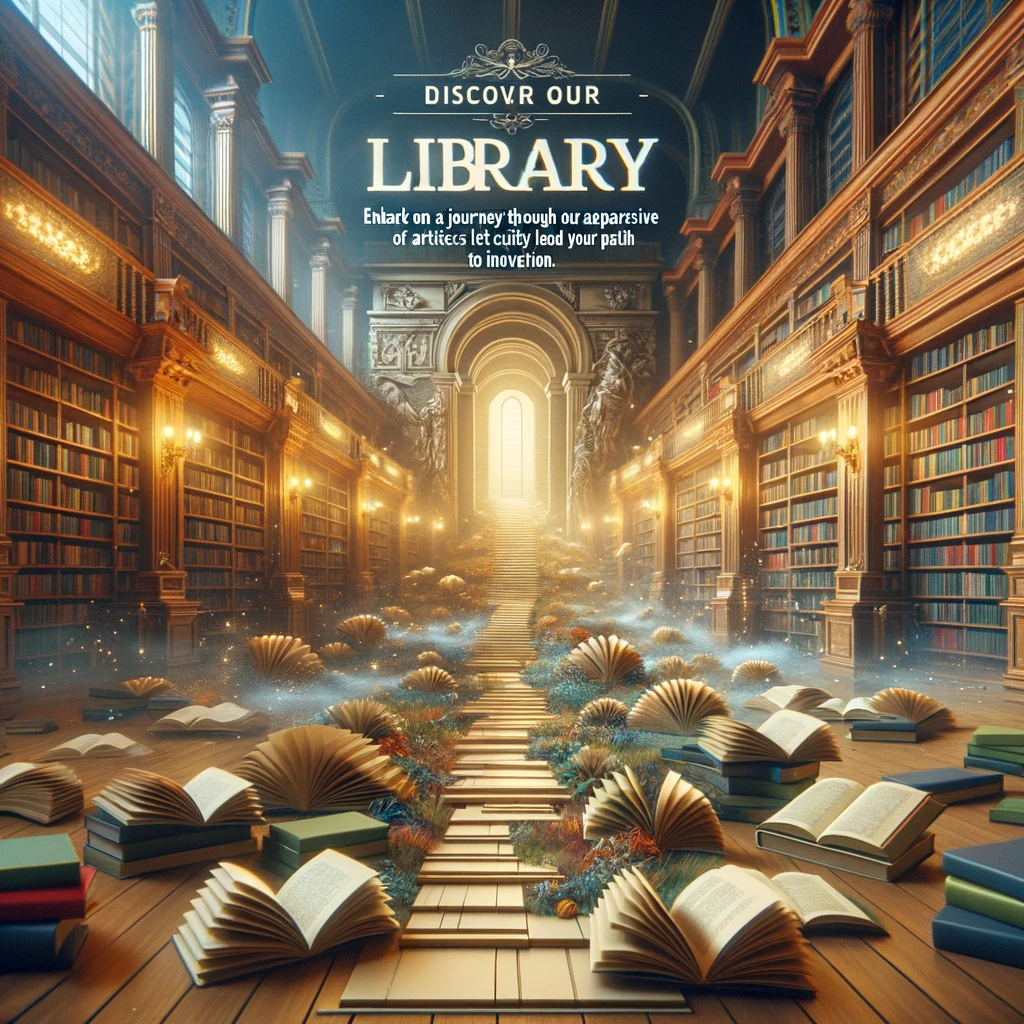